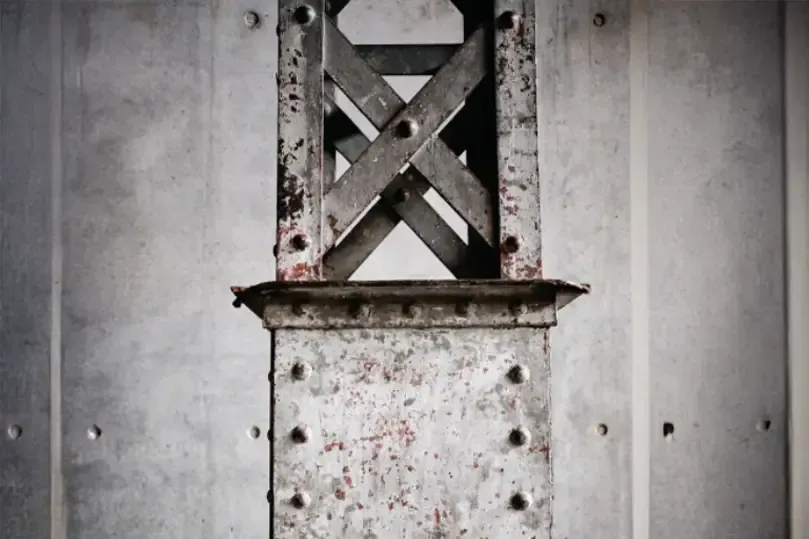
How to Prevent Corrosion in Steel Infrastructure
Steel is a fundamental material in bridges, pipelines, industrial facilities, and municipal infrastructure, but it is highly vulnerable to corrosion. Exposure to moisture, chemicals, and environmental factors can weaken steel over time, leading to structural failure, costly repairs, and safety risks. Preventing corrosion is essential to ensuring the longevity, reliability, and performance of steel infrastructure.
Understanding Corrosion and Its Causes
Corrosion occurs when steel reacts with oxygen and moisture, forming rust that gradually deteriorates the material. Several factors accelerate this process, including:
Exposure to Water & Humidity – Moisture is the primary cause of rust, especially in coastal and high-humidity areas.
Chemical Contact – Industrial environments often expose steel to corrosive chemicals, acids, and salts.
Temperature Fluctuations – Extreme heat and cold can weaken protective coatings, increasing the risk of corrosion.
Pollution & Environmental Contaminants – Airborne pollutants, such as sulfur dioxide, contribute to acidic corrosion.
Mechanical Wear & Damage – Scratches or abrasions can compromise protective layers, exposing steel to corrosion.
Effective Strategies to Prevent Corrosion
1. Apply High-Quality Protective Coatings
One of the most effective ways to prevent corrosion is by applying industrial-grade protective coatings. These coatings act as a barrier, preventing moisture and chemicals from reaching the steel surface. Some of the most common options include:
Epoxy Coatings – Highly durable and resistant to chemicals and moisture.
Zinc-Rich Primers – Provide cathodic protection, preventing rust formation.
Polyurethane Coatings – Offer UV resistance and long-term durability.
Powder Coating – A dry, electrostatically applied coating that protects against wear and corrosion.
2. Use Corrosion-Resistant Alloys
For structures exposed to highly corrosive environments, using stainless steel or galvanized steel can significantly reduce corrosion risks. These alloys contain elements like chromium and zinc, which form a protective oxide layer to prevent rust formation.
3. Implement Regular Inspections & Maintenance
Routine inspections help detect early signs of corrosion before they become major issues. A proactive maintenance plan should include:
✔ Visual Inspections – Checking for rust spots, peeling coatings, or surface damage.
✔ Cleaning & Surface Preparation – Removing dirt, salts, and contaminants that can accelerate corrosion.
✔ Reapplication of Protective Coatings – Repairing worn or damaged coatings to maintain long-term protection.
4. Utilize Cathodic Protection
Cathodic protection is an advanced technique used to prevent corrosion by making steel the cathode of an electrochemical cell. This method is commonly used for pipelines, storage tanks, and marine structures and includes:
Sacrificial Anode Systems – Uses a more reactive metal, like zinc or magnesium, to corrode instead of the steel.
Impressed Current Systems – Applies an external electrical current to neutralize corrosion reactions.
5. Control Environmental Exposure
Minimizing direct exposure to moisture, chemicals, and extreme conditions can significantly slow corrosion. This can be achieved through:
Proper Drainage Systems – Preventing water accumulation on steel surfaces.
Humidity Control – Using dehumidifiers or ventilation systems in enclosed structures.
Protective Enclosures – Installing weather-resistant covers for outdoor steel structures.
The Long-Term Benefits of Corrosion Prevention
Investing in corrosion prevention strategies leads to:
✔ Extended Structural Lifespan – Reduces the risk of premature failure.
✔ Lower Maintenance & Repair Costs – Prevents expensive overhauls and replacements.
✔ Improved Safety & Compliance – Meets industry regulations and reduces hazards.
✔ Enhanced Performance & Reliability – Keeps steel infrastructure strong and functional.
Protect Your Steel Infrastructure with Dun-Right Services
At Dun-Right Services, Inc., we specialize in high-performance protective coatings designed to prevent corrosion and extend the life of your steel infrastructure. Our expert team, industry certifications, and advanced coating solutions ensure maximum protection in even the most challenging environments.
Contact us today to learn how our industrial coatings can safeguard your steel assets for years to come!